CATEGORIES
Time, weather and usage are all contributors to the degradation of silo structures. How often you keep your silo topped off and what kind of material you store can also impact how your silo performs. To keep your silo utilization high and your production goals on target, it's just as important to prevent material flow issues and compaction as it is to address visible damage like cracks, spalling or rust. It's important to observe your silo or storage dome frequently for signs of damage or changes in performance. This helps ensure you catch warning signs early on to address issues before they reach a critical level. However, an in-house silo inspection, cleaning, or repair should never replace professional services. Doing so increases safety risks and can lead to missed or exacerbated issues that may result in structural failure, possible environmental damage, injury, or loss of life.
When it comes to the proper intervals for silo inspections, best practices recommend professional inspections at two- to five-year intervals to help identify any issues that could lead to silo failure. Silo inspections should include examining the main aspects known to be potential areas of failure. These inspections should consist of the foundations, walls, cones, discharge configuration, floors, shelves, tunnels, and roofs.
Experienced silo inspectors or silo engineers can only identify many serious issues during an in-depth examination of silos that are empty and free from material buildup. Therefore, when combined with silo cleaning, however, a professional silo inspection can thoroughly examine the inside of the silo structure, including roof beams and beam pockets, cones, floors, shelves and tunnels for signs of wear or damage.
Sticking to a regular silo inspection schedule with a trusted professional silo inspection company pays for itself. Thorough inspection and silo maintenance, you increase the useful life of your silo, reduce unplanned downtime, and uphold production goals. What's more, the lack of silo maintenance is a leading cause of silo failure.
View our video, How Often Should I Have My Silo Inspected, or view our full library of videos on silo inspection, silo maintenance, and silo restoration on
.
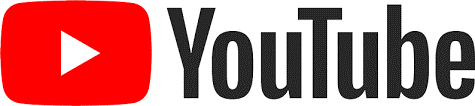
Following a regular inspection schedule ensures the optimal performance of your silo and can help reduce the liability of unexpected failures. It also helps prevent unplanned downtime from unaddressed issues that slow down production, so you keep to your production schedules.
Regular silo inspections can help identify issues to be addressed before they cause irreparable damage. Larger or more extensive silo damage is inherently more costly, and a silo failure can not only impact neighboring silos it can also lead to loss of life. That's why it's essential to get a regular inspection and then follow through with the recommended repairs.
A professional silo inspection examines several areas that are prone to failure. Depending on the level selected, inspection includes an examination of the silo walls, foundation, cones, and roof, concrete sounding to check for signs of delamination, interior inspection, and, if necessary, services of a senior silo design engineer. It's important to make sure your review is performed by a trained professional as they can identify problems missed by the untrained eye.
The Marietta Silos inspection program is designed to meet the needs of any industry. Our three inspection levels, basic, augmented, and comprehensive, can be combined with our latest supplemental inspection service to give you the highest level of flexibility. The AI Supplemental Inspection service can also be used as a standalone service between regular inspections. Using this service annually, you get an accurate, comprehensive portfolio to better track silo defect changes. The AI Supplemental Inspection service brings silo inspection into the 21st-century through the use of drone capture technology, proprietary software, and artificial intelligence (AI) algorithms that identify even the smallest defects, map precise locations, and rank issues in order of severity. It's also the only service of its kind in the U.S., offered exclusively by Marietta Silos.
Contact us today to schedule a silo inspection. When should you schedule a silo inspection? Watch our video, "How Often Should I Have My Silo Inspected?" for more information on determining silo inspection schedules or view our full library of silo videos on
.
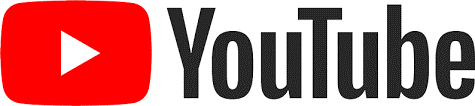
All silos should be regularly inspected whether they are old or new, rarely or frequently used. Identifying potential problems early on through routine inspection can save you big. Silo issues that need to be remediated only become more costly to repair and more dangerous the longer you wait.
Silo Inspection Cost Savings:
- Planned downtime is always far more economical than unplanned downtime.
- Routine repair of a silo will cost you much less than an emergency repair.
- Small repairs are quicker and cheaper than a silo failure.
Ideally, silos should be professionally inspected a minimum of every two to five years. There are, however, conditions that may require more frequent silo inspection, so it's important to know when to schedule a silo inspection.
Professional silo inspection covers more areas of the silo than an in-house inspection. Trained silo inspectors or silo engineers examine your silo(s) in-depth to look for serious issues and provide preventive maintenance suggestions that can help keep your silo in the best shape possible.
When combined with silo cleaning, the inside of the silo structure, including roof beams and beam pockets, cones, floors, shelves and tunnels, can be thoroughly examined for signs of wear or damage.
Sticking to a regular inspection schedule with a trusted professional silo inspection company pays for itself. Through inspection and maintenance, you increase the useful life of your silo, reduce unplanned downtime, and uphold production goals. What's more, the lack of silo maintenance is a leading cause of failure. The costs of keeping up with preventive maintenance are significantly lower than the price of major repairs or construction after a structural failure.
Marietta Silos and USA Silos are the leading industry experts when it comes to silo inspection, cleaning, maintenance, and repair. Contact us today to schedule a silo inspection. To learn more, be sure to check out our full library of silo videos on silo maintenance, inspection and repair on
.
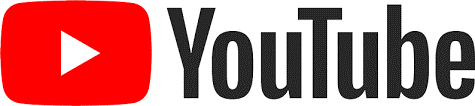